Managing Chemical Challenges in RO Systems: Scale Inhibitors and Aluminum Control – Q&A
- Jeff Yu
- Mar 5
- 6 min read
Q: We are designing a system that needs to operate at 90% recovery due to brine disposal restrictions. My feedwater has a pH of 8 with 0.5 ppm aluminum. What is your recommended Scale Inhibitors and Aluminum Control of the membranes?

Aluminum is extremely insoluble in neutral pH (6-8 pH), especially in natural water sources. A concentration of 0.5 ppm Al at pH 8 is very unlikely. Below is the aluminum pH vs. speciation diagram.
Even though Al is about 85X more soluble at pH 8 compared to pH 6, the solubility is still less than 0.01 ppm at pH 8 (see below table for the maximum concentrations of dissolved aluminum) It is therefore essential to determine how the measurement of 0.5 ppm was obtained to determine aluminum scaling/fouling.
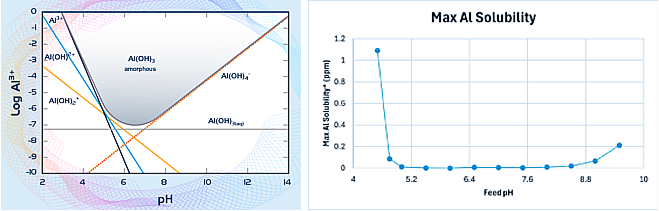
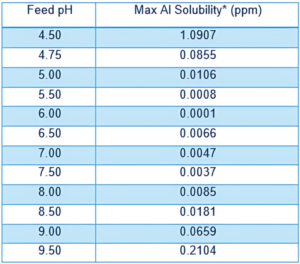
Erroneous aluminum values are often a result of the water collection and analysis procedures. The most common method for analysis of aluminum is total metals by ICP (EPA Method 200.7) Total metals require preservation of the sample and/or digestion by acid to ensure that all metals are dissolved before being analyzed. As many silts and clays are aluminum silicates, acid preservation/digestion can leach aluminum from these silicates into the solution, resulting in a misleading value in the water analysis. Silts and clays will likely be contaminants within the water, regardless of whether the source is groundwater or surface water. Filtration during sample collection would eliminate this problem.
Another source of aluminum may be due to the addition of an aluminum-based coagulant, typically aluminum sulfate (alum) and Poly aluminum chloride (PACl). Once the coagulant reacts with water, colloidal Al(OH)3 particles are formed, and if not fully removed, can foul the RO membranes. Antiscalants can be used to control colloidal aluminum but only within reason. It is unrealistic to expect control beyond 1 – 1.5 ppm Al in the RO concentrate in the neutral pH range. For a system operating at 90% recovery, 0.1 – 0.15 ppm Al in the feed water would be a realistic limit.
This colloidal aluminum can be filtered by MF or UF but would pass through media filtration.
The analysis of filtered water samples, as mentioned above, cannot distinguish between colloidal aluminum from excess coagulant or aluminum silicates. If coagulation is a potential source of high aluminum in the feed water, it’s important to identify it so that the coagulation process can better be optimized. In such a situation, the analysis of filtered samples may be misleading, so it’s always important to compare the analysis of a filtered sample vs. an unfiltered one. The concentration of aluminum in the water analysis would often provide sufficient context, however, when in doubt, the filter can be analyzed by SEM/EDS to determine whether the aluminum was leached from silts/clays or if it was actually in the form of colloidal aluminum hydroxide.
However, there is an exception to this extremely low aluminum solubility. In industrial or municipal wastewater high in organics, the organic acids can form soluble complexes with aluminum. This would be somewhat similar to Al being chelated by EDTA. In such cases, extremely high aluminum values can be measured, and would not be filterable. Therefore, the filtered sample would have a similar or identical value to that of the unfiltered sample. The aluminum can be presumed to be soluble in those situations, and a 0.1 ppm safety value should be entered into the antiscalant projection.
At pH < 5 and pH > 9, aluminum solubility increases dramatically. One useful approach is to enter the water analysis into Proton and check the Scaling Potentials calculations at 0% recovery. If there are no warnings about Al(OH)3 or AlPO4 scale formation, then the aluminum value can be considered realistic. But if Proton gives a warning about the values being above saturation, then the values should be reassessed with the same logic outlined above.
Antiscalants are sensitive to the presence of metals like iron and aluminum, which can either deactivate or taint the antiscalant. It’s important to select the right antiscalant so no aluminum scale or antiscalant fouling occurs.
Q: Under which conditions can antiscalants cause RO membrane fouling?
Reverse Osmosis Antiscalants can cause membrane fouling in Reverse Osmosis systems under the following conditions:
Fungal growth in the antiscalant – some antiscalants contain impurities that can provide the necessary nutrients and carbon for bio-growth. It is not uncommon to find fungal growth in polymer-based antiscalants. The growth in the drum can seed growth on the membrane surface. Reputable manufacturers manufacture higher-purity products and use NSF-approved anti-fungal preservatives to prevent these issues.
The dosing point is too close to the acid addition point – pH is typically adjusted using concentrated sulfuric acid. In the absence of good mixing, the acid will temporarily form a separate phase due to its very high density relative to water. If the antiscalant is dosed immediately after the acid dosing point, it can be hydrolyzed by the strong acid. Certain polymer-based antiscalants are very susceptible to this degradation.
Incompatibility with water quality – some antiscalants do not have a good tolerance to iron and aluminum. Such antiscalants will form an insoluble complex with these metals and precipitate on the RO membrane surface.
Very high hardness or very high antiscalant dosage – antiscalants carry a higher negative charge than typical scale-forming anions such as carbonate or phosphate; so they have a strong attraction to calcium and magnesium. During threshold inhibition, this attraction to calcium/magnesium causes adsorption to form clusters and interferes with the formation of a stable nucleus. However, when hardness concentrations are very high, the antiscalant itself can form an insoluble calcium-antiscalant salt. This is problematic because, once the active inhibitor precipitates, other scales will also precipitate. Hardness impacts all antiscalants, regardless of whether they are polymer or phosphonate-based. Avista’s Advisor Ci antiscalant projection software can predict this salt formation, and can therefore predict maximum recovery at a given temperature and pH.
Quality control issues – in some cases, manufacturing issues can cause certain polymer-based antiscalants to form insoluble gels on the membrane surface. It is therefore imperative to use antiscalants only from reputable suppliers.
Q: What will happen to antiscalants when we discharge them to the environment? Are they toxic? Are they biodegradable? If so how long will they take to decay?
There are different types of antiscalants. Some are phosphonate based,and some are polymer based. Many are blends to provide synergistic effects of the two chemistries. Antiscalants have to be non-toxic, or they would not be approved by NSF for potable water applications. Both phosphonate and polymer based antiscalants are biodegradable over time. Ultraviolet light increases the rate of degradation as the chemical bonds are broken, and certain types of bacteria produce enzymes that cleave the bonds.
Recently some “green” antiscalants have been introduced into the market, with the claim that they biodegrade at a faster rate. In reverse osmosis membrane systems, anything that biodegrades too quickly will be a carbon source for bacteria and contribute to biofouling. It is best to avoid such chemistries from an operational standpoint.
Q: When does it make sense to clean elements, and when is replacement the only option in high-purity applications?
In the case of high-purity applications, the main criterion for clean vs. replace is salt passage. Any increase in salt passage to the demineralized system can be enough financial justification for replacement. As an example, even a slight decrease in salt rejection from 99.6% to 99.2% may not seem troublesome to someone treating brackish water for a potable application. But in a high-purity application that generally employs a mixed bed demineralized system to polish the RO permeate, the amount of salts that have to be removed by the demineralized system would double, which in turn doubles the number of regeneration cycles. This corresponds to a doubling of acid, caustic, and neutralization costs would drive the decision of whether to replace or clean.
Increased salt passage accompanied by increased differential pressure, and/or reduction in normalized permeate flow would suggest that the decline in salt rejection is a result of scaling/fouling and that cleaning may improve permeate quality. However, if permeate quality is not recovered after cleaning, it can be assumed that the loss of salt rejection is permanent and that membrane replacement is necessary.
Comments